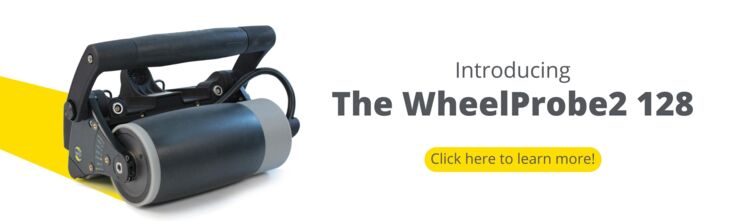
Industries
Latest News
Latest Blog
Exploring the Strength and Versatility of Composite Sandwich Structures
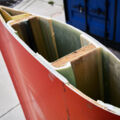
A composite sandwich structure, also known as a sandwich panel, is a type of structural component that consists of two thin, strong face sheets (or skins) on the outer surfaces, with a lightweight,…
Unveiling the Power of Composite Inspection: Enhancing Safety and Performance
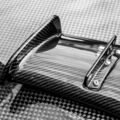
Latest Video
Latest Application Notes
Riser Bolt Inspection with Creo Bolt Scanner
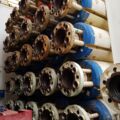
Sonatest performed Phased Array Ultrasonic Testing on one Riser Bolt. A TFM scan was also implemented to increase resolution and flaw fidelity. The bolt can be tested from either end, without removing…
Application Notes
TFMi™ Inspection for monitoring "Blind" Holes
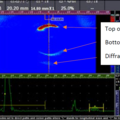
Blind hole inspection is an excellent fit for TFMi™. It really enables a full comprehensive profile view of the internal geometry of a part.
Application Notes
Latest Solution Notes
Ultrasonic Inspection Methods for Composites in Motosports
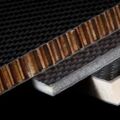
Composites have become a dominant material in motorsport, accounting for up to 85% of the vehicles used today. This includes all levels of Formula racing including F1, as well as Rally car racing,…
Solutions
Advanced Composite Inspection
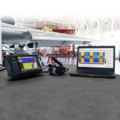
A complete picture of a large component can be produced by stitching C-scans together in the UTmap software.
Solutions
About Us
Pioneering Ultrasonics in NDT Industry.
Whether it is conventional, phased array or FMC-TFM ultrasonic technology, Sonatest is a significant partner in providing Non-Destructive Testing solutions to many industries, including transportation, aerospace, power generation, manufacturing, NDT service and oil and gas to name but a few.
Our products are used by the world's leading companies such as Boeing, Airbus, Shell, Eon, Network Rail and are designed to give the user a powerful tool that is easy to use and will withstand the harsh environments in which NDT is carried out.
Founded in 1958, Sonatest is the third largest UT inspection equipment manufacturer and recognised for the quality of its rugged and portable products all around the world.
Our Services
Non Destructive Testing
Non Destructive Testing, or NDT, is a blanket term for a wide range of analysis techniques used in many industries in order to evaluate the properties of a material or component without damaging it or impairing its properties or performance. There are other terms used to describe this technology, including Non-Destructive Examination (NDE) and Non-Destructive Inspection (NDI).
Due to the fact no harm occurs to the items being tested, NDT is highly valued as a technique for product evaluation and research, often saving time and money. NDT is widely used in construction, aerospace, defence, oil & gas, power generation and medical fields.There are many NDT methods available, each with its own advantages and limitations. Some of the more common NDT techniques include:
- Magnetic Particle Inspection (MPI)
Magnetic Particle Inspection uses a magnetic field to detect surface-breaking discontinuities in ferromagnetic materials. Tiny particles of magnetite (Fe3O4) are applied to the surface of the part, and then a strong magnetic field is applied. If there are any defects on the surface of the part, they will cause the particles to orient themselves in a way that can be detected. - Liquid Penetrant Inspection (LPI)
Penetrant testing, sometimes referred to as liquid penetrant inspection (LPI), is a NDT technique used to detect surface-breaking discontinuities in a material. A penetrant is applied to the surface of the part, and then a developer is applied. The developer causes any defects on the surface of the part to show up as white lines or patches.
- Eddy Current Testing (ECT)
Eddy Current Testing uses the principles of electromagnetism to detect surface-breaking and subsurface discontinuities in non-ferromagnetic materials. A coil of wire is wrapped around the part. An electric current is sent through the wire, creating a magnetic field. This magnetic field creates currents on the surface of the part. The eddy currents cause currents of their own, which create a magnetic field. This field interacts with the original magnetic field, and causes a change in the current. This change can be detected, and can be used to identify when the material changes. - Visual Testing (VT)
Visual Testing is the most common NDT technique, and simply involves looking at the part to see if there are any defects. This is often done in conjunction with other NDT methods, to get a more complete picture of the state of the part.
There are lots of different methods of Non Destrucve Testing available. Different techniques will suit different applications, so it is important to choose the appropriate testing method for the task in hand. Here at Sonatest, we offer instruments to use in a range of different ultrasonic evaluation techniques, including thickness gauging, flaw detection and phased array examination. We also offer comprehensive tools to work with the equipment including relevant sowftare, couplants and accessories.