Ultrasonic Inspection Methods for Composites in Motosports
Composites have become a dominant material in motorsport, accounting for up to 85% of the vehicles used today. This includes all levels of Formula racing including F1, as well as Rally car racing, Moto GP, Karting and many more.
Inspections on and off the track can help in identifying damaged parts in need of repair or replacement, identifying manufacturing defects laminations, poor bonding, porosity etc. All of these help teams be better informed when making the fast decisions needed in the pit lane and help with the design and verification of each component of the vehicle.
Composites can account for up to 85% of cars used in motorsport today, this includes all levels of Formula racing up to F1, Rally car racing, Moto GP, karting and many more.
With composites being used in safety critical impact zones, high temperature areas, areas requiring low weight and flexibility it is more important than ever to have methods of testing the integrity of these parts to ensure driver safety and get the best performance out of the car. When racing series also enforce budget caps or constraints, it forces teams to preserve or repair their parts rather than replacing them after suffering damage or a set number of uses, inspection allows teams to make this decision with more information on the integrity of the part under consideration.
The following inspection solutions are available over the Sonatest ultrasonic inspection range of products, to find out what solution is best for your composite inspection requirements contact the applications team at applications@sonatest.com
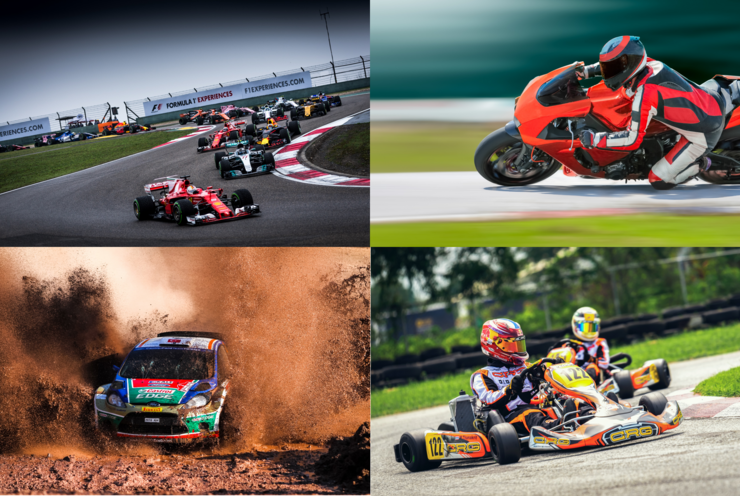
What is a composite?
A composite material is a combination of two or more materials with different physical and chemical properties that when combined create a material with specialised properties, these can be anything from overall strength, flexibility in defined planes, electrical resistance, high temperature resistance and many more.
In motorsports the use of many different types of composites can be found all over the vehicles fulfilling different specific tasks.
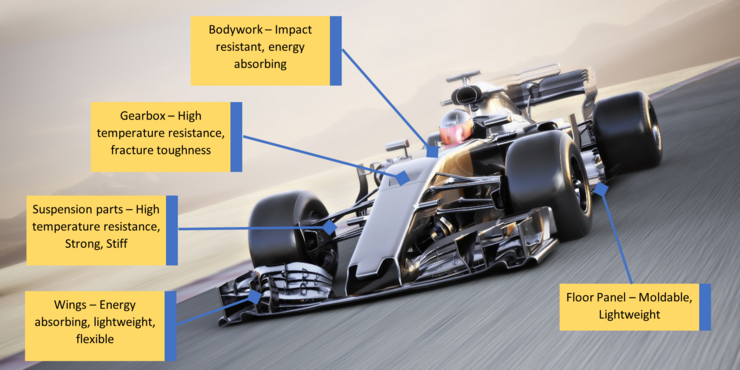
Example of composite uses and properties on a race car
Inspection challenges
Composites use multiple layers of materials often layered with fibres in different orientations and formed into complex geometry shapes, these characteristics which make composites perfect for racing applications also make the inspection of these parts more complicated than homogeneous materials like metals and plastics. This means the inspection solutions need to be as versatile as the composites themselves.
Non-woven and woven fibre composites
Non-woven fabrics include the likes of glass fibre matt which comprises of chopped strands of glass fibres that are held together in a random orientation by a chemical binder. Woven fabrics include carbon fibre and Aramid fibre sheets. In woven fabrics there are a variety of ways in which the yarns can be weaved to align the fibres in the precise orientations required for optimum mechanical performance. Woven reinforcement fabrics are mostly used in bodywork.
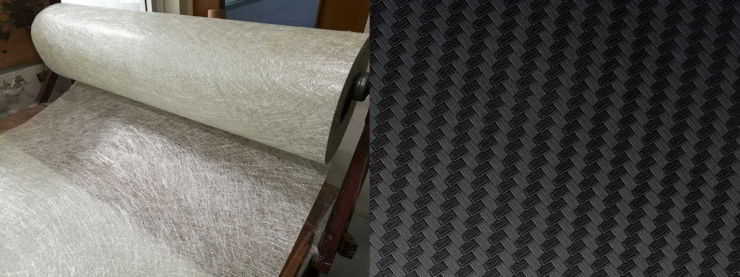
None woven fibre matt and woven carbon fibre sheet
Uni directional composites
Uni-directional fabrics include glass, carbon or aramid and are made up of fibres running in the same direction. This method allows for several layers of uni-directional fabric to be aligned exactly as required and in the desired quantity to achieve a composite with incredible strength which is why uni-directional fabrics are used in suspension components. These layers can then be held together by additional stitching, a binder or a resin.
Sandwich Structures
To increase the stiffness of a laminate you could add more layers, however, if you were to double the thickness of the laminate in this way, you would also double the weight. To work around this, plies can be bonded to either side of a lightweight core material, creating a sandwich structure.
Although this dosent't quite achieve the level of stiffness of doubling the number of plies, it can lead to significant increase in stiffness with almost no addtional weight. Core materials used in motorsport are usually either aluminium or Nomex honeycomb but foam cores are also used, These cores dissipate the majority of the shear stresses and dure to its ability to absorb energy through deformation under failure, offers high impact resistance. It is this structure which allows the material to be extremely light for a given stiffness and strength, adding to its suitability for race car bodywork and chassis parts.
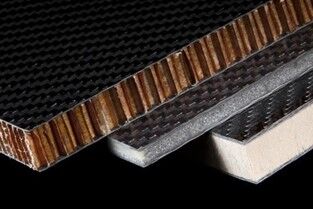
Examples of composite sandwich structures
Composite defects
Composite defects most commonly form during the manufacturing process the most common of which are as follows:
- Delamination of layers
- Bonding defects
- Porosity / voids
- Ply cracking
- Layer deformation
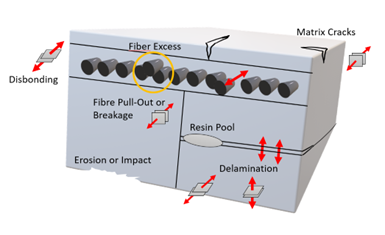
Composite defects
These defects can also be caused by in service use and impacts, these are mostly detected visually with obvious visible damage like cracking or loss of material, but not all defects are visible from the surface and require a method of inspecting the internal structure of the composite to ascertain if that part is fit for service. See below for a table of common defects and where they can occur.
Defect | Composite laminates and bonded joints | Sandwich structure |
---|---|---|
Delamination | Can occur between ply layers | Can occur in the ply plates on either side of the sandwich structure |
Disbonding of ply layers | Can occur between ply layers due to poor bonding material application | Can occur between the ply and core materials |
Porosity / voids | Can occur anywhere between layers where air has been trapped or the bonding agent has not been mixed properly | Can occur in the ply plates on either side of the sandwich structure |
Impact damage | Cracking, delamination through multiple laysers can be caused by impacts | Cracking, disbonding and delamination through multiple layers can be caused by impacts |
Deformation in ply layers (wrinkling) | Poor application of ply layers can cause deformation of the composites sheet between layers | Can occur in the ply plates on either side of the sandwich structure |
Table 1 - composite defect types and where they can occur

C-Scan images of common composite defects

Typical composite defects and the ultrasonic sound paths used to detect them.
Inspection Solutions Available
Phased array L-Scan inspection
A highly versatile scan, phased array L-Scanning of composites allows for adjustable aperture sizes and a range of frequencies, This method is able to penetrate the multiple layers of composites to detect internal defects at all levels of the material and can allow the inspector to view individual layers of a structure. Additionally data can be viewed in amplitude and depth views both giving different insights to the condition of the part.
An L-Scan can be carried out using phased array transducers in contact with the surface or with wheel probes, both of these methods allow scans to be made of the material that can be stitched together to form a full picture of a part as a merged C-Scan.

Phased array probes used for L-Scans, WP2, X3 Glider, X6B with bubble column
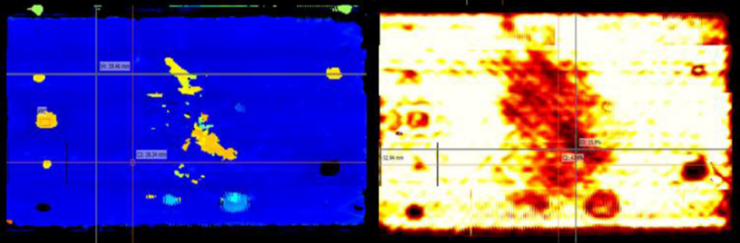
Wheel probe merged C-Scan showing depth view (left) and Amplitude view (right) of a simulated impact damage plate.
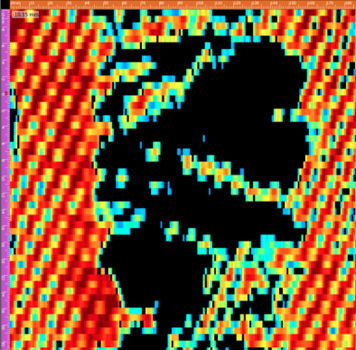
L-Scan single C-Scan image of a sandwich structure showing an area of disbonding between the top ply and honeycomb core
Through Transmission techniques
Through transmission is a technique where two probes are placed either side of a material, one probe will transmit the signal and the other will receive the signal on the other side. This can be carried out using conventional single crystal probes or specially designed ‘Dryscan’ probes as detailed below.
Often called the ‘shadow technique’ a received signal shows that the sound has successfully travelled through the full material without interruption, a loss of signal indicates the signal has been stopped within the material by a defect, plotting of the area of lost signal will locate and size the defect area.
Dryscan Probes
Dryscan low frequency probes are designed to be used without couplant and are often used to inspect honeycomb structures. This method can detect delamination of the plate or disbonding of the plate to the core material, moreover this technique can detect defects in the honeycomb structure itself.
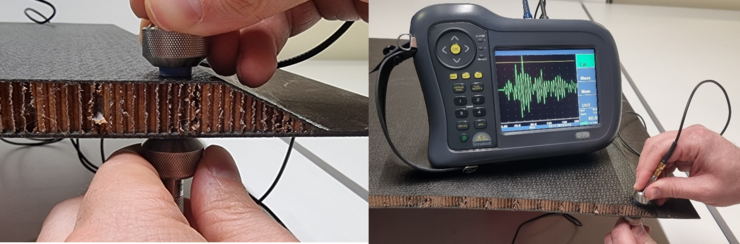
Dryscan through transmission of composite honeycomb sandwich structure
Recommended Package
Category | Part Number | Description |
---|---|---|
Product | VEO3, PRISMA, RSFLITE, WAVE | Phased array aquisition units for all inspection configurations, conventional ultrasonic inspection units |
Probe | WP2, PA probes, Dryscan probes, conventional UT probes | Probe selection to be defined by the required solution. |
For further information, please contact the Sonatest Sales Team