PAUT of Welds to 2020 AWS D1.1
7th June 2023
Will Haworth
Sonatest
As of 2020, per AWS D1.1, PAUT is now an acceptable testing method for Structural Steel welds with a thickness between 3/16” and 8”, using an encoded linear scan.
Conventional Ultrasonic Testing (UT) has been the go-to method for volumetric testing of structural steel welds for decades. In 2015, AWS included Phased Array Ultrasonic Testing (PAUT) as an accepted testing method in the D1.5 Bridge Welding Code, and then added it to the 2020 D1.1 Structural Welding Code – Steel. PAUT offers many benefits over conventional UT and has become one of the major testing methods in most other industries including ASME piping and pressure vessels, API pipelines and tank structures, and more. PAUT scans can be performed much faster than convention UT scans because there is no rastering involved. Because of the permanent record obtained with PAUT, the weld does not need to be evaluated at the time of scanning, and this data is available for future reference (similar to an X-Ray film). By utilizing an S-Scan, and B or C-Scan, you can create a 3-dimensional image of the flaw, rather than just an A-Scan view, which can be used to better characterize and size a flaw, and is much easier for non-UT professionals to understand. Each PAUT report will include a “Scan Plan” comprised of all pertinent UT setting and parameters, so each scan is highly repeatable.
We will focus on Annex H of the 2020 D1.1:
“H1. Introduction. This annex provides mandatory requirements that shall apply when phased array ultrasonic testing (PAUT) is used. The alternative techniques presented in this annex require written procedures, advanced personnel training and qualification, and calibration methods specific to PAUT.”
Equipment Requirements:
Annex H of the 2020 D1.1 requires the following equipment for PAUT of welds:
Minimum 16 channel PAUT Instrument
A, B, C and S Scan Views
Encoding Capabilities
Minimum 16 element Probe, 1-6 MHz
Angled Wedge producing 40-70° Shear Waves
Both the Sonatest Veo3 or Prisma meet these criteria, as well as several of our X2 or DAAH series probes and wedges:
- X2A-001 – 5MHZ 16 Elements
- X2B-001 – 5MHZ 32 Elements
- X2B-005 – 2.25MHZ 32 Elements
- X2B-006 – 5MHZ 64 Elements
- D1A-001 - 2.25MHz 20 Elements
- D1A-002 - 5MHz 32 Elements
The X2AW-N55S, X2BW-N60S, and D1AW-N57S wedges would accompany these probes.
The AXYS Encoder meets the requirements to encode a line scan. Many other scanners can be provided for plate or pipe welds.
Personnel Requirements:
Current Level II UT inspectors only need 320 work time experience hours in PAUT, and to pass a practical exam on 2 flawed samples.
Calibration:
Calibration Blocks such as the IIW Type 2 and/or NavShips block can be used for verifying and calibrating the setup. The AWS Supplemental Reference Block combines the IIW and NavShips blocks. Angle Beam, Horizontal Sweep (Angle Sensitivity), TCG, and Sensitivity (Reference Level) can all be created or verified on this one Reference Block.
For Sensitivity, the SSL (Standard Sensitivity Level) must be determined by peaking the .060” side drilled hole on the IIW block.
Examination:
Once a Scan Plan is created to include weld thickness and geometry, focal law(s), index position(s), focusing, and other ultrasonic settings, the weld can be scanned. The welds are to be scanned at the at the SSL, or 6db above the SSL. Each scan must be encoded, and data recorded. A maximum of 1% data loss is allowed.
Evaluation:
H10.3 Acceptance Criteria. Welds shall be acceptable provided they have no planar indications, nor any indications whose amplitude or length exceeds that specified in Table H.2 for the applicable type of loading. Discontinuities shall be classified based on their maximum amplitude in accordance with Table H.3 (also see Figure H.4):
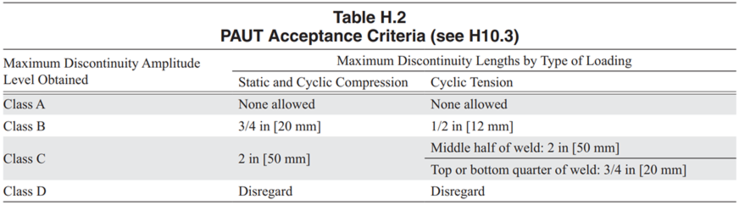
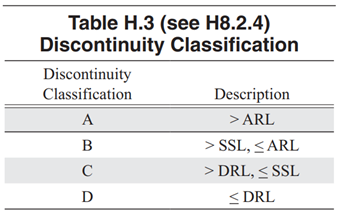
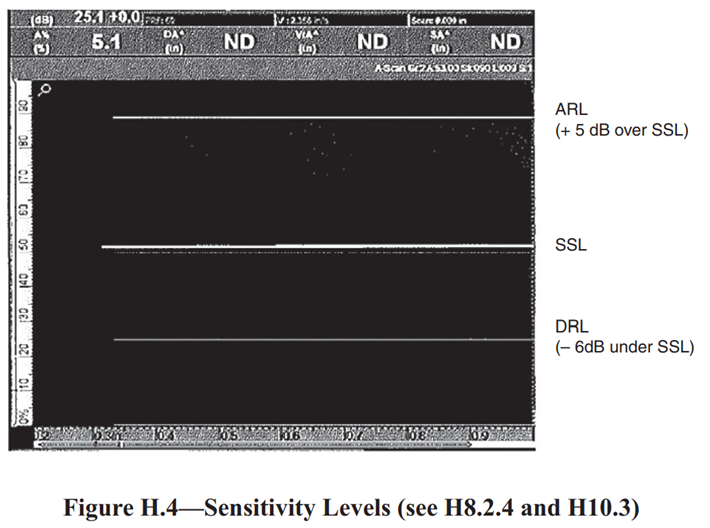
Indications lengths shall be determined by using the 6 dB drop rule.
Scan Data:
Data can be analysed for acceptance either on the instrument itself, or on post-analysis software.
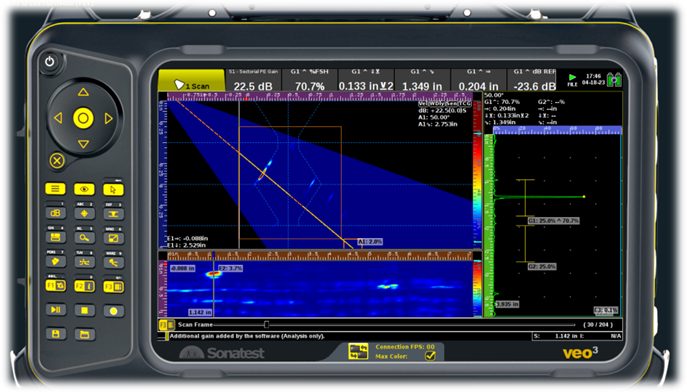
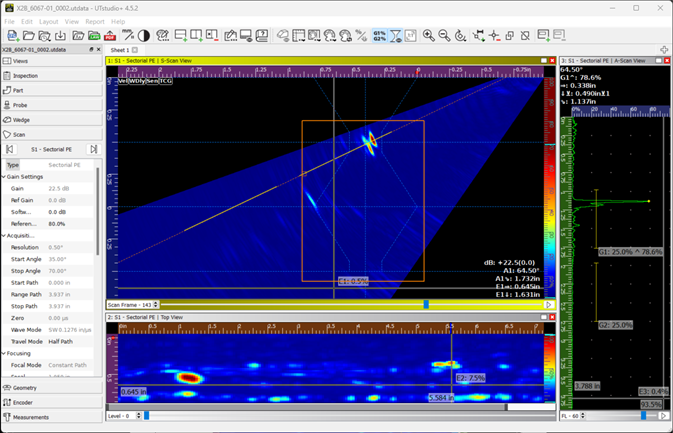
Conclusion:
With the inclusion of PAUT in the 2020 AWS D1.1 code, you can achieve improved scans of welds in less time, significantly increasing productivity and efficiency. These recorded scans will be available for review any time after the scan is performed, and include 3D views of any discovered flaws that can be clearly interpreted by UT inspectors, engineers, project managers, welders, and anyone else involved in the welding process.
Recommended Tool Package
For further information or support, please contact the Sonatest Sales Team sales@sonatest.com